EPS Volume Reduction Machine—High MelterRE-E1000
High throughput, safety and workability
in a space-saving machine with
all the necessary functions.
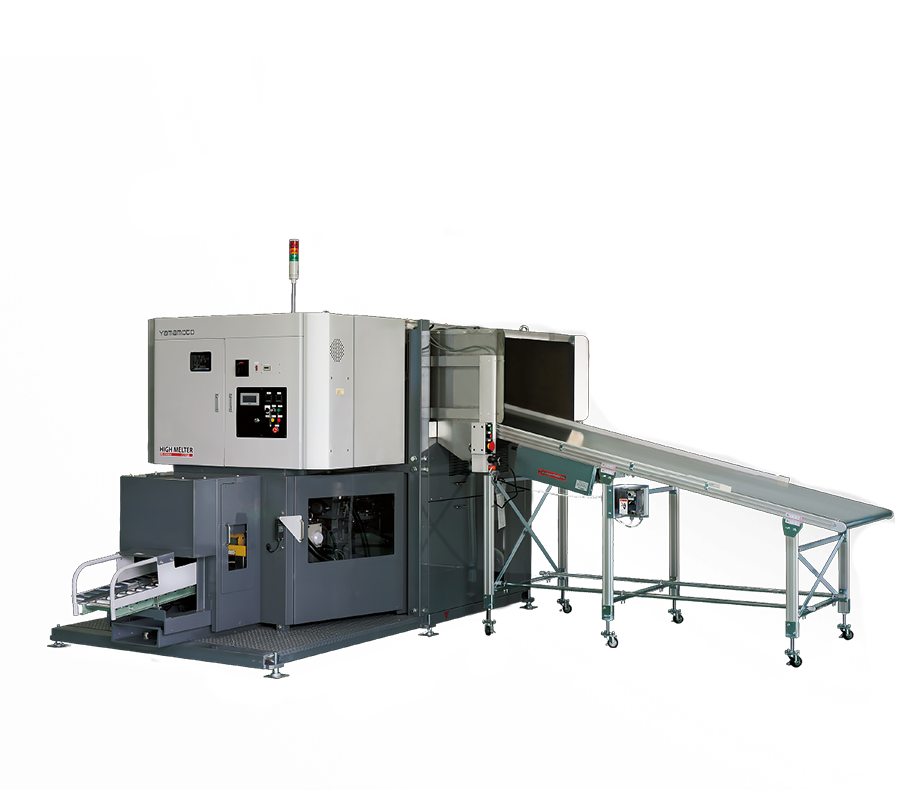
Object to be processed
-
EPS
Expanded
polystyrene -
PSP
Polystyrene
paper -
XPS
Extruded
polystyrene -
EPP
Expanded
polypropylene -
EPE
Expanded
polyethylene
Recycling Process
RE-E1000 Product Introduction Video
Why Yamamoto?
We're all about making work
safe and comfortable.
While our machines provide unrivalled performance
and create the
highest quality ingots,
our real focus is on workplace safety, comfort, and ease
of use.
Easy & Simple
Operation
Our machines are designed to be easy for anyone to use. For regular operation, simply touch a button and watch as ingots are automatically formed and cut to the specified size.
Reduces
Work-Related Stress
The warm-up time is only 15 minutes. There is no need to keep the operator waiting before starting operation or resuming after a break. If the optional Automatic Ingot Aligner is installed, the operator does not need to pick up each ingot because it automatically arranges the cut ingots. This frees the operator to focus on feeding raw materials into the machine, and thus it can process a higher volume faster.
Consideration for
the Working Environment
The small heat source makes it difficult for odours to diffuse, and an activated carbon deodoriser is fitted as standard. Also, the crushing hopper is equipped with sound-absorbing material, which significantly reduces noise. This promotes a comfortable working environment.
Configuration
The Hi-Melter RE-E1000 is a compact machine with a volume reduction capacity of 100 kg per hour designed to promote a safe and comfortable working environment.

Click on a part's name for details.
1
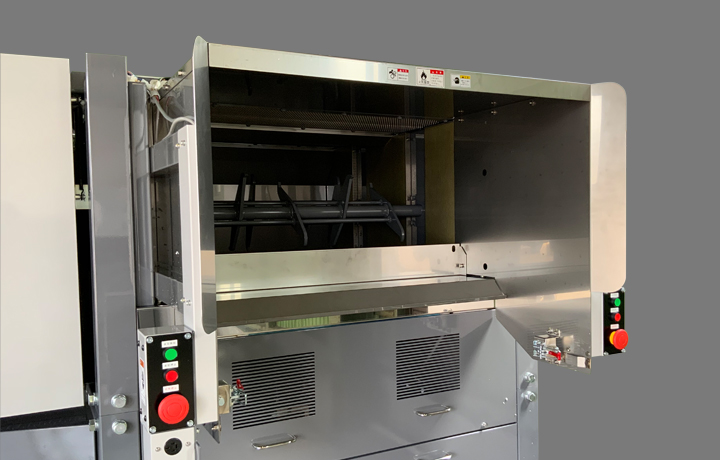
Feeding Hopper
The hopper has a feeding width of 1,000 mm, is made of corrosion-resistant stainless steel and is equipped with sound-absorbing material which significantly reduces noise pollution.
2
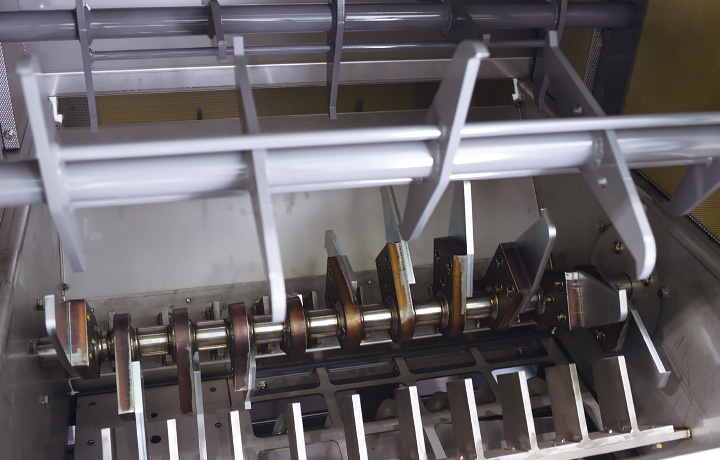
Crushing Section
The crushing blade is our proprietary design and crushes all kinds of styrofoam such as fish boxes, cushioning materials and trays.
3
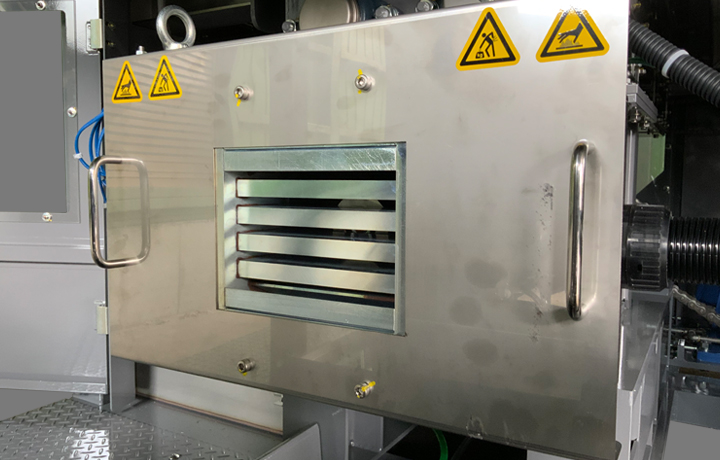
Electric Heater
Warm-up operation time is 15 minutes.
Since the volume is reduced in
a short time at a low temperature of 200℃, ingots are formed that are of
higher quality and with less deterioration of physical properties.
4
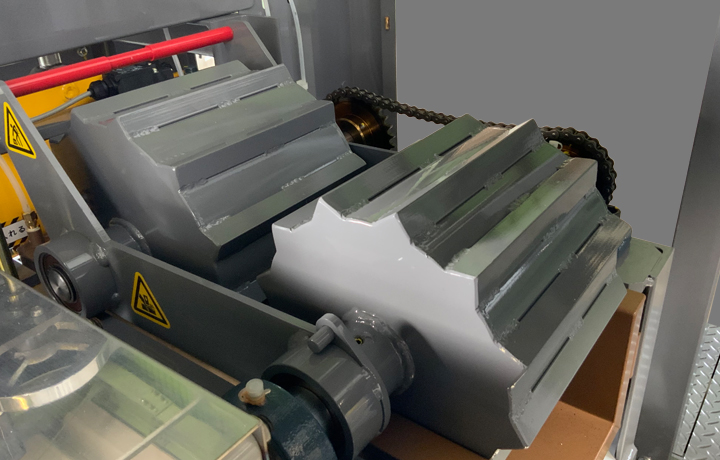
Molding Section
Expanded polystyrene melted from the heater is formed into the specified shape by forming rolls and stamps, air cooling with a blower, and water cooling with a molding sink. A cooling water circulation system is adopted to eliminate the need to worry about drainage.
5
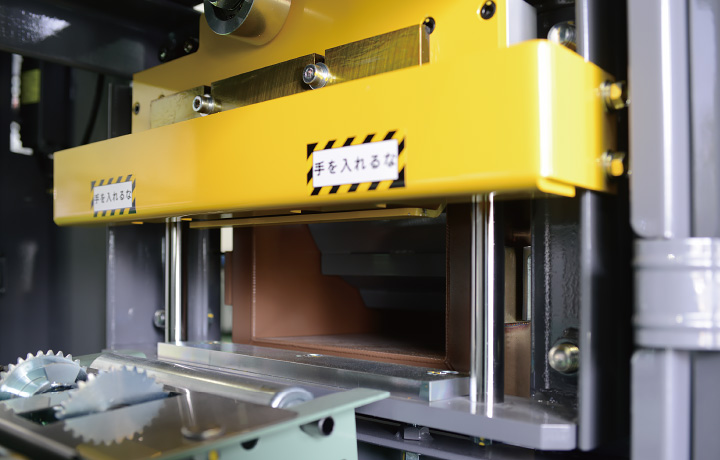
Cutting Section
The wheel sensor monitors the discharge of ingots, and the cutting blade automatically cuts them to the specified length (400, 600, 800, or 1,000 mm).
6
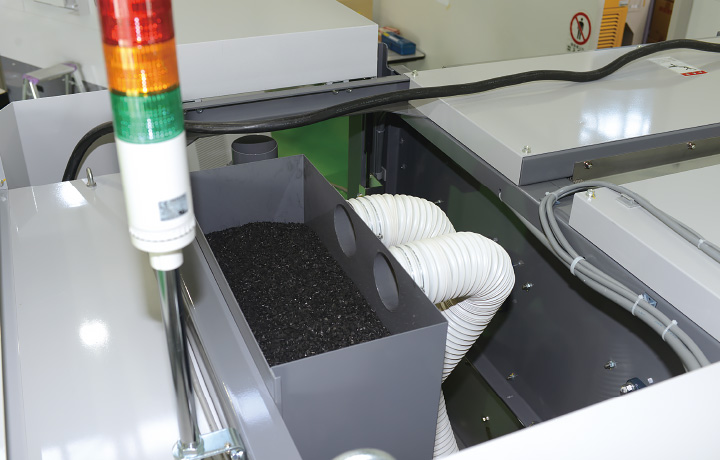
Deodoriser
It deodorizes the odour generated at the time of volume reduction by activated carbon adsorption method and promotes a comfortable working environment.
7
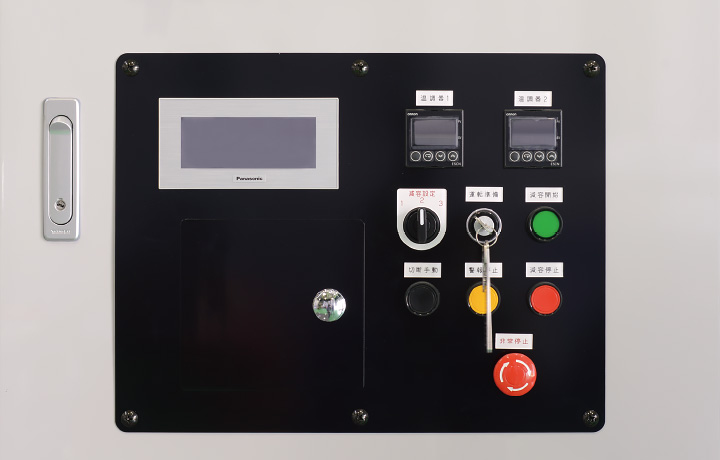
Control Panel
Precise and meticulous temperature control is possible. In the event of a problem, the operator will be notified by an alarm sound, alert light, and error message displayed on the monitor.
8
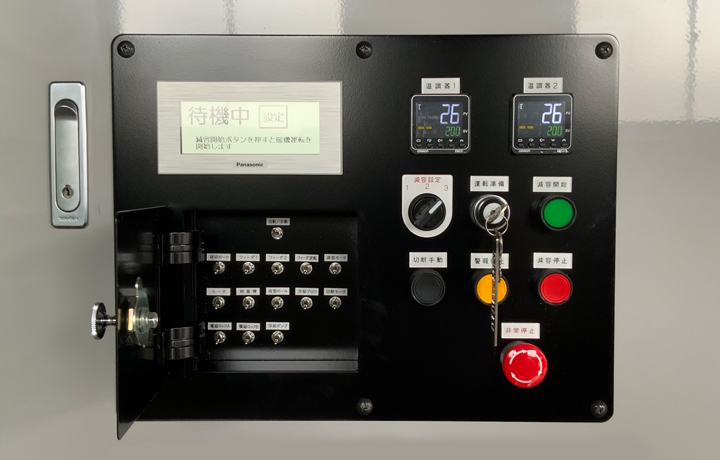
Manual Operation Switch
A maintenance switch is located inside the panel. By switching to manual operation, the individual motors can be operated separately, e.g. during maintenance.