EPS Volume Reduction Machine—High MelterRE-E502(X)
A long-time seller chosen by companies from a broad range of industries,
this machine sets the standard for volume reduction machines.
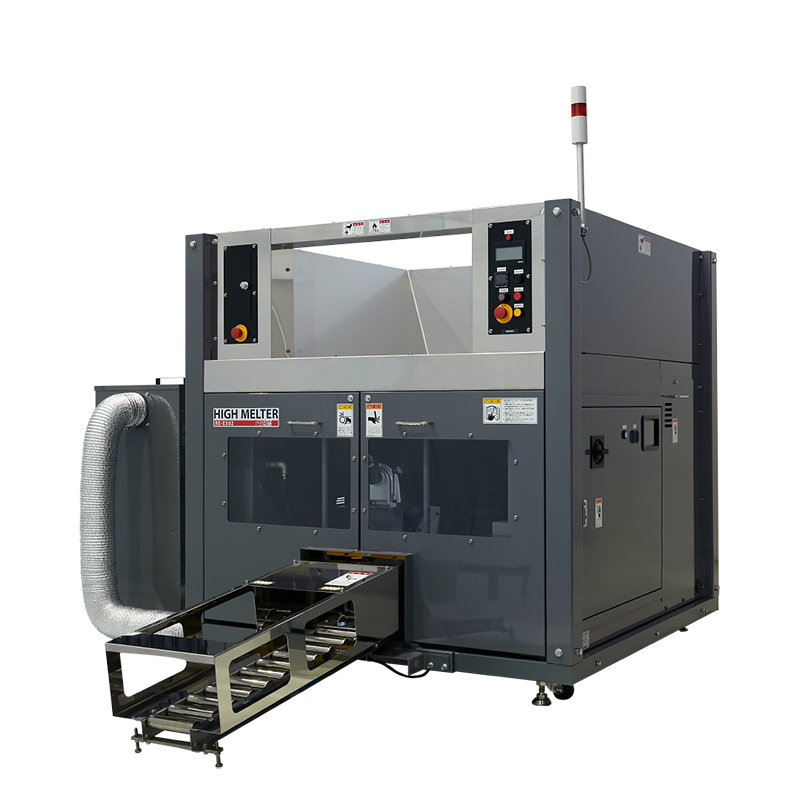
Object to be processed
-
EPS
Expanded
polystyrene -
PSP
Polystyrene
paper -
XPS
Extruded
polystyrene -
EPP
Expanded
polypropylene -
EPE
Expanded
polyethylene
Recycling Process
RE-E502(X) Product Video
Why Yamamoto?
We're all about making work
safe and comfortable.
While our machines provide unrivalled performance
and create the
highest quality ingots,
our real focus is on workplace safety, comfort, and ease
of use.
Easy & Simple
Operation
Our machines are designed to be easy for anyone to use. For regular operation, simply touch a button and watch as ingots are automatically formed and cut to the specified size.
Reduces
Work-Related Stress
Warm-up time is only 10 minutes. There is no need to keep workers waiting when starting work or when resuming work after a break. Furthermore, it is unnecessary to cool the ingot by immersing it in water by air cooling with a cooling blower and water cooling with a molding sink.
Consideration for
the Working Environment
The small heat source makes it difficult for odours to diffuse, and an activated carbon deodoriser is fitted as standard. This promotes a pleasant working environment.
Configuration
The Hi-Melter RE-E502 (X) is
a compact machine with a volume
reduction capacity of 50 kg per hour.
It is designed for safe and comfortable
operation.
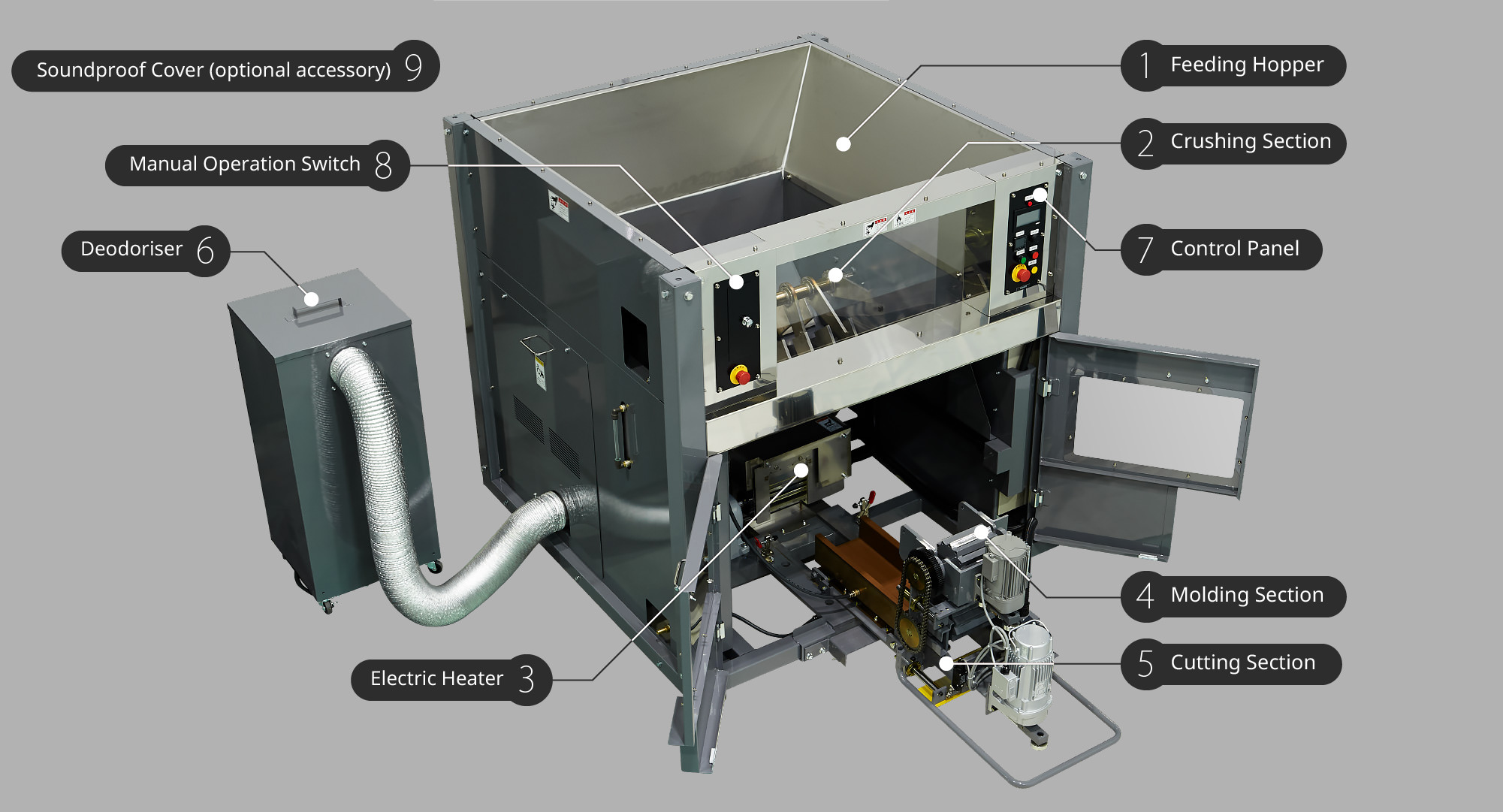
Click on a part's name for details.
1
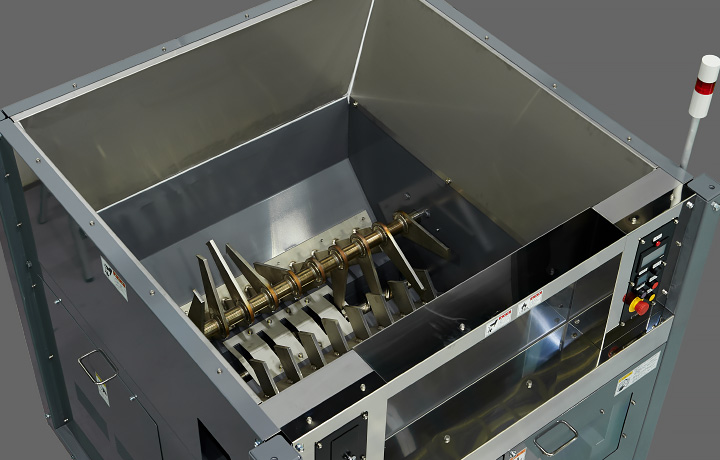
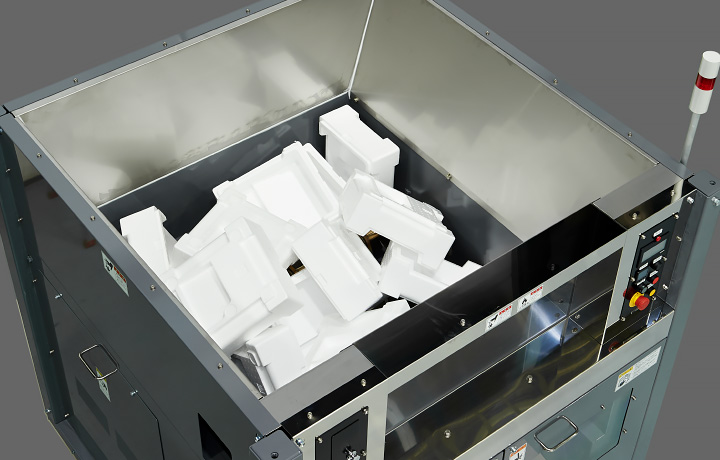
Feeding Hopper
The wide hopper is large enough to hold 10–20 fish boxes. The continuous feeding system keeps the work area clean and saves space.
2
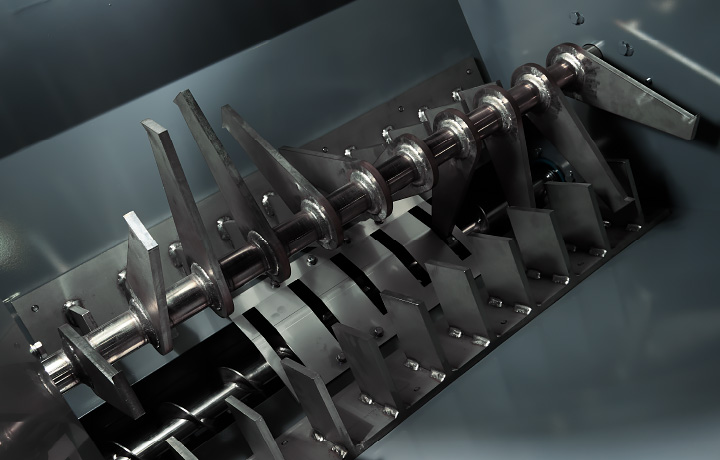
Crushing Section
The crushing blade is our proprietary design and crushes all kinds of styrofoam such as fish boxes, cushioning material, and trays.
3
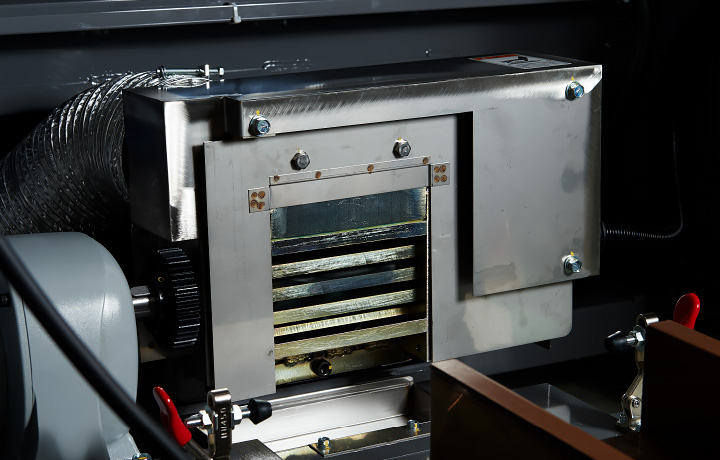
Electric Heater
Warm-up operation time is only 10 minutes.
Due to the low temperature
of 170°C and rapid volume reduction, ingots are of higher quality and
less deterioration of physical properties.
4
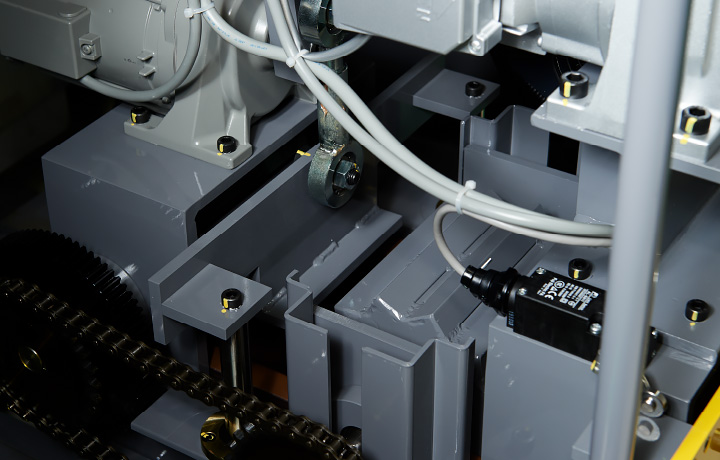
Molding Section
Expanded polystyrene melted from the heater is formed into the specified shape by forming rolls and stamps, air cooling with a blower, and water cooling with a molding sink. A cooling water circulation system is adopted to eliminate the need to worry about drainage.
5
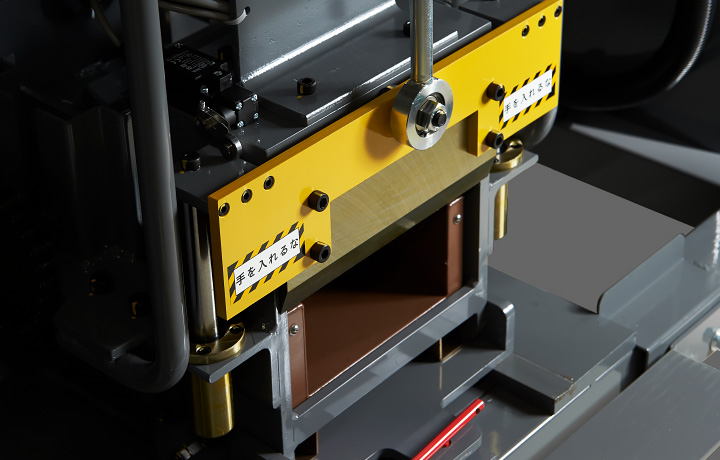
Cutting Section
The wheel sensor monitors the discharge of ingots, and the cutting blade automatically cuts them to the specified length (adjustable between 470–1,100 mm).
6
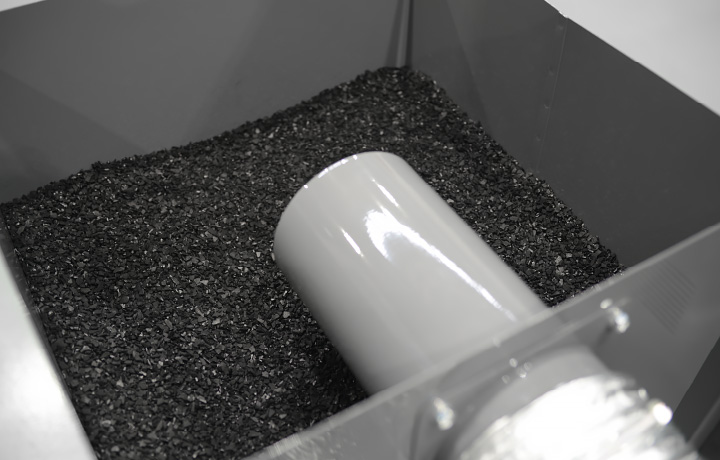
Deodoriser
The deodorizing system uses an activated carbon adsorption system to remove odours generated during volume reduction and promote a comfortable working environment.
7
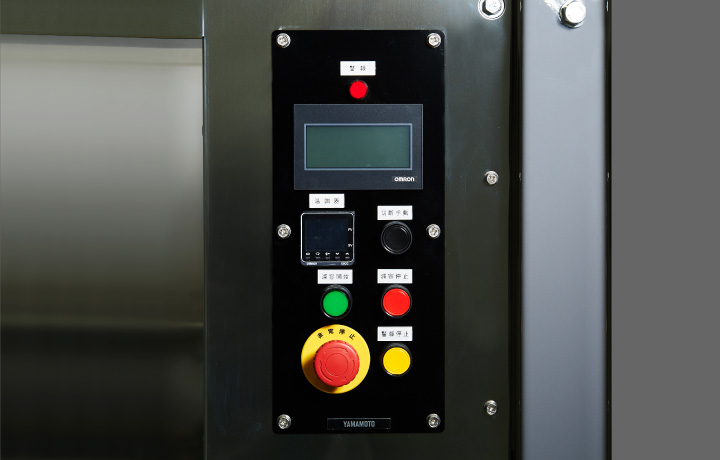
Control Panel
Precise and meticulous temperature control is possible. In the event of a problem, the operator will be notified by an alarm sound, alert light, and error message displayed on the monitor.
8

Manual Operation Switch
A maintenance switch is located inside the panel.
By switching to
manual operation, the individual motors can be operated separately, e.g.
during maintenance.
9
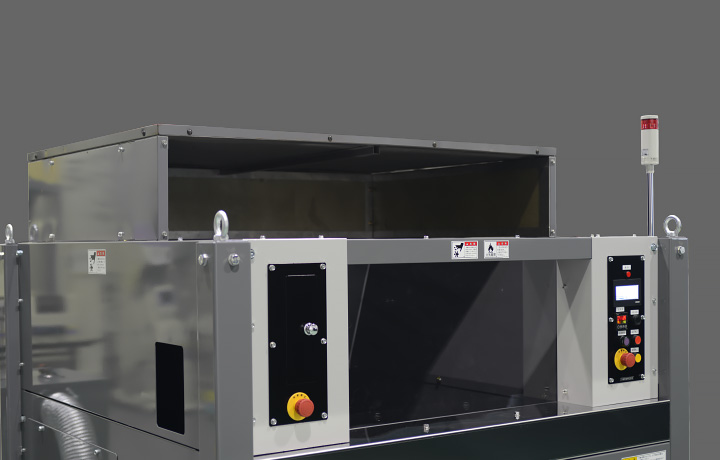
Soundproof Cover (optional accessory)
The soundproof cover significantly reduces the noise level during crushing and prevents noise pollution of the working environment.